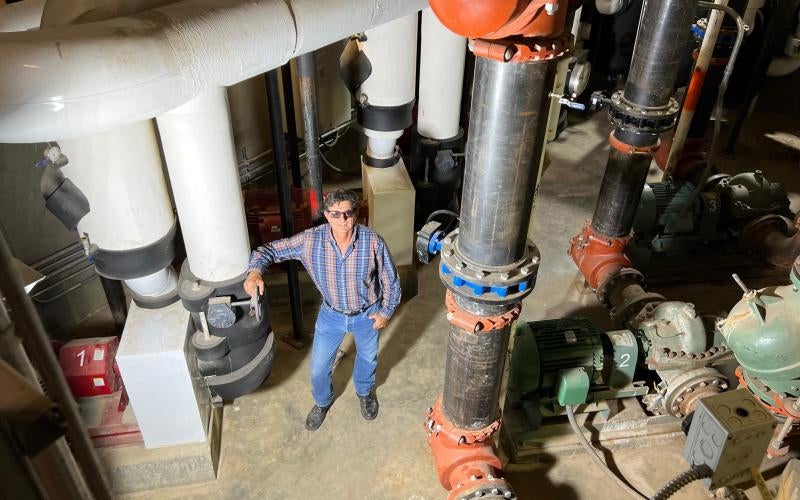
Steve Eckert recognized by Department of Energy as national industry expert
September 11, 2023Arizona Western College included on DOE’s Best Practices in District Energy list
Yuma, AZ (September 11, 2023) – Steve Eckert, Arizona Western College Director of Facilities Management, was recently honored by the U.S. Department of Energy as one of nine engineers and facilities leaders to be featured on the department’s national Directory of Experts.
Along with the recognition, Eckert and his team’s energy saving efforts landed AWC on the DOE’s Best Practices in District Energy list for 2023. The list was created by the DOE through a cooperative agreement with the International District Energy Association to study and catalog organizations that had the best practices in enhanced resiliency, efficiency, and carbon reduction. As a result of the two-year study, AWC earned recognitions in all three areas: engineering, operations, and finance.
“In facilities, we have a saying, ‘The easy day was yesterday.’ We run into new challenges every day that most of the campus community is unaware of because we mitigate them before they impact the learning environment. It feels good to be recognized for those behind-the-scenes efforts,” said Eckert.
Eckert has been working at AWC since 2011 and has over three decades of experience in facilities management and project engineering. Over the last 10 years, AWC has grown to include a new Public Safety Institute and multiple building additions (Welding, Theater, Engineering Building, Library) as well as the addition of many high-technology systems in a number of classrooms and labs. With all of these new uses, the amount of energy expended would have dramatically increased, but through cost savings efforts, 35% less electricity was used in FY 22/23 than in FY 12/13.
“The efforts of Steve Eckert and his facilities team have had a significant impact on the fiscal health of the college budget over the years. As our institution continues to grow and expand its facilities, these cost-saving measures will be an invaluable asset moving forward,” said Ross Poppenberger, AWC Vice President of Finance & Administrative Services.
Eckert’s areas of expertise consist of technical best practices like chilled water system optimization, cooling tower upgrades, solar power purchase agreements, and thermal energy storage as well as management and financial best practices including his work on service contracts, preventative maintenance, and a “Turn it off” marketing campaign.
AWC consists of 37 buildings (roughly 650,000 square feet) and hosts over 11,000 students and 400 faculty and staff. It is one of the only community colleges in the country to offer on-campus housing (348 beds). To keep its facilities up and running, the campus is served by a central plant and a chilled water loop that rotates usage between three 800-ton chillers.
Technical Best Practices
Chilled Water System Optimization
In 2014, AWC’s food service provider Sodexo approached the college with a proposal from Flow Energy, an energy optimization consultant, to analyze and optimize the campus’s chilled water system. At the time, the campus was running all three of its chillers during the summer. This was a concern as Yuma’s extreme summer temperatures would require the campus to evacuate if a cooling system went down. At the same time, the campus was also adding square footage and the price of utilities was increasing.
After conducting a site survey, the consulting firm made upgrades to the system that allowed AWC to recover 600 tons of stranded cooling capacity, which AWC used to add three new buildings to the chilled water system; they received 2.5 million kWh of electricity savings and 15 percent reduction in peak demand charges; earned a $275,000 utility rebate; and improved cooling temperatures to free up their third chiller and pump during the summer.
Cooling Tower Upgrades
The college’s facilities budget is split between utilities and basic campus improvements such as roof and parking lot repair. The majority of the department’s infrastructure projects are funded through revenue bonds, such as a recent cooling tower replacement project. Though AWC’s original cooling towers had been upgraded with new, larger fans, they lost significant capacity through rapid corrosion and evaporation. In 2021, college leadership approved a plan to purchase three new cooling towers for the campus. The college is anticipating these new towers to produce an additional 500 tons of cooling.
Solar
AWC installed 5 MW of solar PV in 2011, financed via Power Purchase Agreements. Since then, the array has generated more than 60 million kWh and saved the campus more than $4 million in electric utilities. AWC has also negotiated an extremely favorable 1-for-1 net metering contract with APS.
Thermal Energy Storage
In addition to optimization and solar installation, AWC has repurposed existing infrastructure to generate additional energy savings. The campus has a 300,000-gallon underground tank that had been used for condensing water and was switched to a chilled water system in 2014. With the added capacity AWC avoided turning on their second chiller until June this year and was able to load shift out of peak hours all summer by charging the tank at night and discharging for 3-4 hours in the afternoon.
Management and Financial Best Practices
Service Contracts
By 2014 the college realized it would need to make a major investment in their cooling system, and they were presented with a cashflow-friendly opportunity. AWC’s food service provider partnered with an energy optimization contractor and approached the college with a proposal: the college could fund the optimization project by marginally increasing the payments for their existing food service contract. Spreading the costs out through an existing budget line item was integral for getting approval for the project, especially as energy savings started to hit the facilities budget.
Preventative Maintenance
AWC has a robust preventative maintenance program, supported by a work order system that automatically schedules out the next instance of any given activity based on the day the activity was completed. This accommodates late afternoon and evening activities and prevents the next round from being performed too early.
A vital component of AWC’s afternoon and evening program is coil cleaning. Since the Yuma Campus is adjacent to both a desert and an agricultural facility, airside loading of cooling coils is high. In order to maintain efficiency, the coils must be regularly, and thoroughly cleaned. The college noticed a stark difference in cooling efficiency when the coils started being consistently cleaned.
“Turn it off” Marketing Campaign
Before AWC started addressing its energy efficiency concerns, lighting was a significant but preventable drain on the campus’s energy. In many buildings, lights were on 24-7; in some cases, they couldn’t be turned off at all. The facilities team started by installing lighting controls, including switches and timers, in all buildings and beginning to migrate over to high-efficiency bulbs and followed up with a marketing campaign designed to encourage occupants to turn off lights when leaving the room. The facilities team noticed a significant change in campus behavior and consider this program a major contributor to the larger energy efficiency effort.
Eckert and his facilities team were recently featured in the digital magazine Blueprint for their energy saving efforts. The story can be found at this link.
Contact:
Lori Stofft
Vice President for Advancement and Executive Director for the AWC Foundation
Arizona Western College
Lori.Stofft@azwestern.edu
928-314-9595
Contact:
Steve Eckert
Director of Facilities Management
Arizona Western College
Stephen.Eckert@azwestern.edu
(928) 314-9475